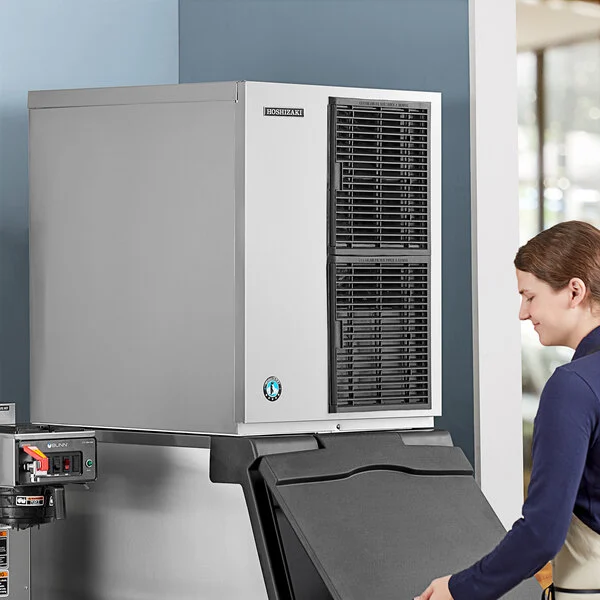
Hoshizaki Ice Machine Not Producing Ice
Many factors can cause your Hoshizaki ice machine to stop producing ice. Here are a few things you can check to diagnose the issue:
Check the power supply and fuse. If the ice machine is not starting, check if it is plugged in and switched to the ON position. Also, check if any loose connections need to be tightened and if the voltage is too high and needs to be replaced. If everything looks okay, check for a blown fuse. Replace the electrical panel if it has a short circuit.
Check and clean the float switch. If the float switch is sticking, it may be due to scale build-up. Clean the float switch with ice machine cleaner and check the operation with an ohm meter. If the problem persists after cleaning, replace the float switch.
Check your compressor. Clean your condenser’s air filter if it is clogged and dirty. Replace any loose connections. If your compressor is defective, call your service agent to replace it.
Check your refrigerant. The unit will not run properly if the refrigerant is undercharged or overcharged. Recharge if necessary.
Check if your control board is functioning properly. If you suspect your control board is defective, reference your service manual to perform a control board check. Replace if necessary.
Hoshizaki Ice Machine Not Producing Enough Ice
Several factors can lead to the under-production of ice. Many ice production issues stem from the environment your ice machine is located.
Deep clean the machine. Verify that the evaporator, condenser, air filter, water filter, and water valve are clean before conducting a production check. Low ice production could be caused by buildup, so it’s important to regularly deep clean your ice machine.
Check the room temperature. Maximum ice production for each machine is partially calculated based on the room temperature where the unit is located. If your location exceeds the suggested temperature, the machine will not be able to produce the maximum amount of ice. The recommended room temperature for maximum ice production is 70 degrees Fahrenheit.
Check the water temperature. Check the incoming water temperature and the ambient condensing temperature of the unit. If the water used to make the ice is too warm, ice will not form properly.
Hoshizaki Freeze Cycle Longer than Normal
Long freeze cycles can also result in low or abnormal ice production. Here are a few steps you can take to diagnose this issue.
Clean the float switch. If the float switch is sticking, it may be due to scale build-up. Clean the float switch with ice machine cleaner and check the operation with an ohm meter. If it still does not check properly after you clean it, replace the float switch.
Check your water valve. A leaking water valve will lengthen the freeze cycle. Clean the bleed port in the valve diaphragm, replace the diaphragm, or replace the water valve.
Check your refrigerant. Check for leaks and recharge if necessary.
Hoshizaki Ice Machine Freezing Up
When dealing with a freezing ice machine, the most important element to check is the evaporator plate. It is recommended to defrost and clean the ice maker before diagnosing freeze-up.
Defrost and clean the ice maker. Defrost the unit to check if the evaporator plate has mineral or scale buildup. If buildup is present, clean the water system with Hoshizaki SCALEAWAY, following the instructions provided on the cleaner’s label.
Check the waterline size. Confirm that the waterline is of adequate size. An undersized waterline, as well as an undersized water inlet valve, can contribute to a freeze-up.
Look for frozen waterlines. Frozen waterlines are common in extremely cold regions or during winter months. Call a plumber right away if you notice frozen waterlines.
Look for obstructed waterlines. Obstructed or clogged waterlines can be caused by scale or mineral buildup. Call a plumber to have obstructed waterlines professionally cleaned.
Check the water flow rate. Verify that the incoming water flow rate matches what your ice maker needs. If you find the water flow is reduced, check the external water filters and replace them as needed.
Check if your control board is functioning properly. If you suspect your control board is defective, reference your service manual to perform a control board check. Replace if necessary.
Mold in Hoshizaki Ice Maker
Molding in an ice machine can be common if the machine is in an unsuitable environment. It can also be caused by infrequent or improper cleaning.
Sanitize the bin. If you find mold in your ice bin, deep clean and sanitize the unit per the cleaning and sanitizing instructions provided in your unit’s manual.
Ensure your staff is properly handling ice. Make sure your staff is always handling ice with an ice scoop and never their hands or used glassware. Clean the ice scoop every night.
Consider moving the unit. Keep your machine away from any areas of your kitchen that are more conducive to mold. This includes prep stations that handle large amounts of dough, yeast, sugar, or any ingredients that thrive in environments with lots of moisture.
Hoshizaki Ice Machine Leaking
Leaks that appear outside the ice machine are most likely a plumbing issue related to the machine not being installed properly. This fix will require a plumber. If the leak is coming from inside the machine, call an authorized ice machine technician to fix the issue. Turn your machine off before inspecting it to avoid accidents or electrical injur
Check the shutoff valve. If the origin of the leak is the water shutoff valve, attempt to contain the leak to avoid water damage and call a plumber to rectify the problem.
Look for drain obstructions. Check the drains and clear any obstructions.
Inspect the water line. Similar to water shutoff valve malfunctions, a cracked or loose water line requires the help of a plumber to get your machine working back to normal.
Deep clean the machine. Once a plumber has come to fix the unit or you have managed to dislodge anything blocking the drains, deep clean your machine to ensure there are no other buildup issues.
Why Is My Hoshizaki Ice Cuber Beeping?
Hoshizaki ice cubers have an audible alarm safety system that features several beep patterns associated with specific issues, allowing you to quickly and easily identify the problem your ice machine is facing. The number of beeps will be every 3 seconds. For flakers and specialty ice units, reference your model’s service manual for specific error codes.
1 Beep: High Temperature Safety Warning
To prevent damage to the unit, the machine will shut down if the thermistor reaches a temperature over 127 degrees Fahrenheit. Complications with the hot gas valve (HGV), hot water entering the unit, or a shorted thermistor are the most common factors causing this issue.
2 Beeps: Harvest Cycle Back Up Timer
The control board has a defrost backup safety timer that protects from long harvesting. This alarm is warning you that the machine ran two 20-minute harvest cycles in a row. An open thermistor, thermostatic expansion valve (TXV) leak, the HGV not opening, low refrigerant charge, and defective compressor are the most common factors causing this issue.
3 Beeps: Freeze Timer
The control board will shut down if the freeze time is longer than the set time for two freeze cycles in a row. A closed float switch (in the up position), leaking water inlet valve, leaking HGV, low refrigerant charge, and defective compressor are the most common factors causing this issue.
4 or 5 Beeps: Short Circuit or Open Circuit
The 4-beep alarm will sound if there is a short circuit between the K4 connection on the control board and the bin control. The 5-beep alarm will sound if there is an open circuit between the K4 connection on the control board and the bin control. Check the connections and replace the wire harness if necessary.
6 or 7 Beeps: Low Voltage or High Voltage
When the voltage is below 92 volts +/- 5 percent, a 6-beep alarm will sound and the control board automatically will shut down. The machine will restart once the correct voltage is restored. When the voltage exceeds 147 volts +/- 5 percent, a 7-beep alarm will sound and shut down the unit. The machine will restart once the correct voltage is restored.
To reset the above safeties, press the “ALARM RESET” button located on the cuber’s control board with the power supply on.
Hoshizaki Ice Machine error codes:
Error Code | Problem | Corrective Action/Reset Details |
E1 | Freeze Cycle Backup TimerFreeze cycle backup timer (Control Board Setting 6) has terminated.45 min. after water tank starts to close in preceding harvest cycle, unit stops if the evaporator temperature is above 32°F (0°C). | Check for inlet water valve leaking by, hot gas valve leaking by, pump motor not pumping, thermostatic expansion valve not feeding properly, low charge, or inefficient compressor. Press the “RESET” button to reset. |
E2 | Harvest Cycle Backup TimerHarvest cycle backup timer has terminated.30 min. after water tank starts to open in harvest cycle, unit stops if harvest cycle termination temperature (Control Board Setting 1) has not been reached. | Check for open thermistor, HGV not opening, TXV leaking by, low charge, or inefficient compressor. Press the “RESET” button to reset. |
EE(E3) | Water Tank Opening Backup Timer3-minute opening backup timer starts when water tank starts to open.If actuator motor’s internal position sensor does not indicate water tank is fully open within3 minutes, display shows “EE” and unit stops for 60 minutes.If error recurs after unit resumes operation,display shows “EE” and unit shuts down. | Check actuator motor and control board. Press the “RESET” button to reset. |
EE(E4) | Water Tank Closing Backup Timer3-minute closing backup timer starts when water tank starts to close.If actuator motor’s internal position sensor does not indicate water tank is fully closed within3 minutes, display shows “EE” and unit stops for 60 minutes.If error recurs after unit resumes operation,display shows “EE” and unit shuts down. | Check actuator motor and control board. Press the “RESET” button to reset. |
EE(E5) | High Evaporator TemperatureIf evaporator temperature 140°F (60°C) or higher for 5 sec., unit stops. | Check for harvest problem (stuck HGV or control board relay), hot water entering unit, or shorted thermistor. Press the “RESET” button to reset. |
EE(E9) | Condenser Thermistor ErrorIf condenser thermistor is open or shorted for 2 sec., unit stops.Note: IM-500SAA does not utilize a condenserthermistor, therefore E9 error will not occur. | Replace condenser thermistor. |
EE(EA) | Control Board ErrorIf model data IC is defective, unit stops. | Replace control board. |
EE(EC) | Evaporator (Cube Control) Thermistor Error If evaporator thermistor is open or shorted for 2 sec., unit stops. | Replace evaporator thermistor. |
EE(Ed) | Water Regulating Valve ErrorIf water regulating valve thermistor detects a temperature below the water regulating valve error detection temperature (Control Board Setting 36), error is displayed but unit continues to operate.Note: IM-500SAA does not utilize a waterregulating valve, therefore Ed error will not occur. |
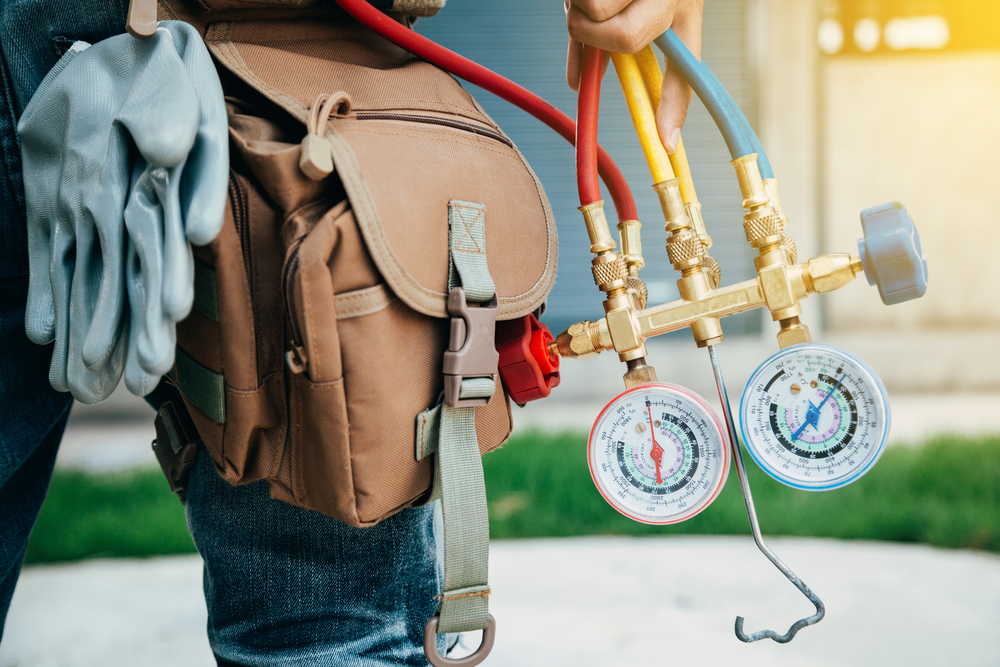
JK HVAC We install, repair and service all brands of air conditioners! Including air conditioner cleaning, dryer vent cleaning, furnace repair.
📍 Serving all of New York City: Manhattan, Brooklyn, Staten Island, Queens…