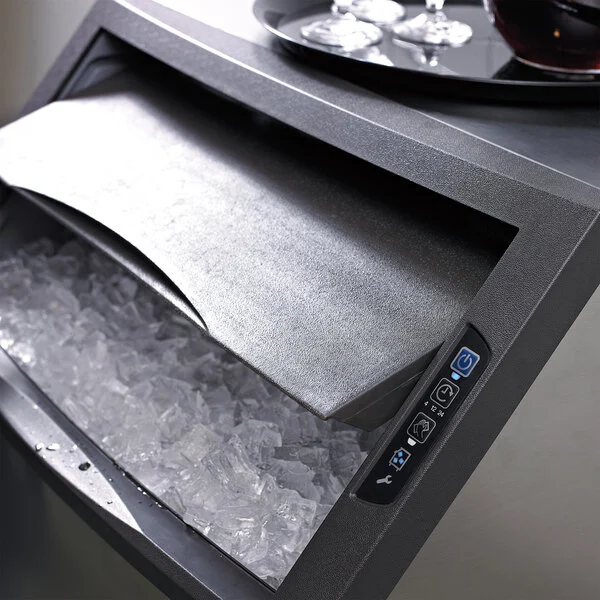
Manitowoc Ice Machine Not Working
If your ice machine does not turn on or is failing to operate correctly, here are some simple fixes to troubleshoot before calling for service:
Check if the ice machine is getting power. Make sure your unit’s power cord is plugged into the correct receptacle. This may seem like an obvious one, but it’s always good to double-check. Press the On/Off button to start ice production. A blue light will indicate that the machine is on and in ice-making mode.
Check the breaker. Take a look at your breaker box. Reset the breaker if it’s tripped and replace a fuse if it’s blown.
Check if the water curtain/ice damper is in the open (downright) position. The water curtain/ice damper must be in an upright position and capable of swinging freely.
Manitowoc Ice Machine Is Not Making Ice
If your ice machine does not release ice or does not cycle into harvest mode, here are some troubleshooting tips to look for:
深度清洁机器。 Keeping a clean unit is important in nearly every aspect of producing ice. No or low ice production could be caused by buildup, so it’s important to regularly deep clean your ice machine.
Level the machine. Another cause of disproportionate ice production could be the surface your unit rests on. Ensure that the machine sits balanced and level on the floor or countertop and that there is adequate clearance around the machine.
Check for low air temperature. The air temperature surrounding your unit must be at least 35-40 degrees Fahrenheit depending on the unit for it to function properly.
Check the water regulating valve. Replace the water regulating valve if it is leaking in harvest mode.
Check the harvest float switch. If the harvest float switch is dirty, clean the component. If the wire is disconnected, connect the wire. Adjust the switch if it’s out of adjustment.
Check the ice thickness probe. If the ice thickness probe is dirty, clean the component. If the has become disconnected or is out of alignment, reconnect to the control board or readjust.
Manitowoc Ice Machine Is Not Making Enough Ice
Several factors can lead to the under-production of ice. Many ice production issues stem from the environment in which your ice machine is located. We’ve listed some troubleshooting tips below to run through, but it is also a good idea to go through the tips listed in the “Manitowoc Ice Machine Is Not Making Ice” section above.
检查室温。 Maximum ice production for each machine is partially calculated based on the room temperature where the unit is located. If your location exceeds the suggested temperature, the machine will not be able to produce the maximum amount of ice. For most Manitowoc units, the maximum air temperature is 110 degrees Fahrenheit.
检查水温。 The recommended water temperature is 48-50 degrees Fahrenheit. If the water used to make the ice is too warm, the ice will not be able to properly form.
Check the water pressure. Your water pressure may be too low – it should be between 20-80 PSI.
Check the water filter. Change the water filter if it’s dirty or broken.
Check the condenser. A dirty condenser will affect ice production, so clean it if necessary. Also, verify there are no items stacked around the ice machine that could be blocking airflow to the condenser.
Check the water supply. Make sure your water supply is connected and the water service valve is open.
Manitowoc Ice Machine Is Leaking Outside the Machine
If your Manitowoc ice maker leaks water, follow the steps below to troubleshoot. Most of the time, the issue needs to be rectified by a plumber.
- Turn off your machine before inspecting. Avoid any potential accidents or electrical injury by unplugging your machine before looking for the source of the leak. This may also prevent the leak from expanding.
- Inspect the machine to determine the source of the leak. Depending on the leak’s origin, you may need to call a technician or a plumber. Frequently, leaks on the outside of the machine are caused by plumbing issues.
- 检查截止阀。 如果泄漏的源头是断水阀,请尝试控制泄漏以避免水损坏,并致电水管工来解决问题。
- 查找排水管堵塞情况。 检查排水管并清除所有障碍物。
- 检查水管。 与水截止阀故障类似,破裂或松动的水管需要水管工的帮助才能使您的机器恢复正常工作。
- 深度清洁机器。 Once a plumber has come to fix the unit, or you’ve managed to dislodge anything blocking the drains, deep clean your machine to ensure there are no other buildup issues.
Manitowoc Ice Machine Is Leaking Inside the Machine
Leaks can occur just as often inside the machine as outside. However, inner leaking should most likely be attended to by a technician. Safely inspect the machine to determine the source of the leak and call your technician for a tune-up if necessary.
Manitowoc Ice Machine Is Freezing Up
When dealing with a freezing ice machine, the most important element to check is the evaporator plate. Freezing can damage the evaporator plate irreparably and be costly to fix if a technician or a plumber is not called to inspect the machine. There are a few steps you can take to prevent freezing.
Clean the machine and use a descaler. If your unit is located in a region with hard water, mineral or scale buildup may be causing the machine to freeze. Clean the machine using a descaler that is safe for ice machines to get rid of the buildup and prevent freezing.
寻找结冰的水管。 在极寒地区或冬季,水管结冰很常见。如果您发现水管结冰,请立即联系水管工。
寻找堵塞的水管。 水管堵塞可能是由水垢或矿物质堆积造成的。请联系水管工,请专业人员清理堵塞的水管。
Manitowoc Ice Machine Error Codes
All Manitowoc NXT models come equipped with a series of service codes and notifications to inform you of any potential issues with the machine. These codes are helpful to pinpoint any issues before they become serious or damaging to the unit. However, many of these codes will require a visit from a technician to avoid significant damage or machine failure. Below is a quick guide to Manitowoc’s error codes.
- E01 – Long Freeze Cycle
- E02 – Long Harvest Cycle
- E03 – Input Power Loss
- E04 – High Condenser Temperature
- E05 – High Pressure Control Opened
- E07 – Starving TXV Single Evaporator or Low On Charge
- E08 – TXV Fault Single or Dual Circuit Evaporators
- E09 – Flooding Evaporator Fault Single Evaporator, Single Circuit
- E10 – Flooding Evaporator Fault Dual TXV, Dual Circuit
- E11 – Refrigeration Fault Curtain Fault
- E12 – Curtain Switch Fault – Open more than 24 hours
- E15 – Fan Cycle Control Fault – Low Liquid Line Temperature
- E16 – Remote Condensing Unit Fault (CVD Only)
- E19 – Ice Thickness Probe Fault
- E20 – Water System Fault
- E21 – T1 Temperature Sensor Issue
- E22 – T2 Temperature Sensor Issue
- E23 – T3 Temperature Sensor Issue
- E24 – T4 Temperature Sensor Issue
- E25 – Bin Level Probe Low Sensor Fault
- E26 – T6 or T7 Temperature Sensor Issue
- E27 – T6 or T7 Temperature Sensor Issue
- E28 – iAuCS
- E29 – USB Communication Fault
- E30 – USB Download Fault
- E31 – Safe Mode
- E32 – RS485 Communication Fault
- E33 – Touchscreen Fault
- E34 – Display Fault
- E36 – Check Sum Error
- E37 – Watch Dog Event
- E38 – UI Comm Event
Manitowoc Safe Mode
Certain Manitowoc ice makers are equipped with a safety operation mode that enables the ice machine to function for up to 72 hours in the event of an ice thickness probe or water level probe sensor failure.
The control board will automatically activate safe mode, displaying an alert on the screen to notify the operator of the issue. If the problem is resolved, the control will exit safe mode on its own. However, if the issue persists for over 72 hours, the control board will switch to standby mode and power down. To operate in safe mode, the control board requires a history of five cycles. If the ice machine has not completed five cycles, it will just shut off.
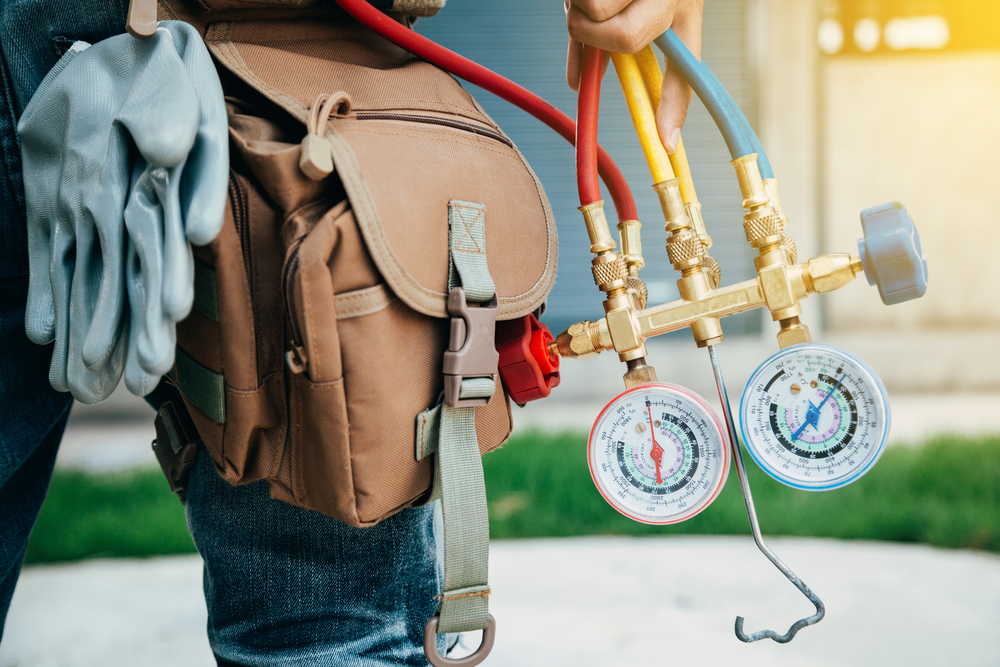
JK HVAC 我们安装、维修和保养所有品牌的空调!包括空调清洁、烘干机通风口清洁、暖气炉维修。
📍 服务纽约周边地区:曼哈顿、布鲁克林、史坦顿岛、皇后区……快速上门估价